Aluminum Nitride(ALN)
Aluminum nitride(AlN) has high thermal conductivity and electrical insulation, and can be used in various electrical equipment. In addition, the thermal expansion coefficient and electrical insulation properties of aluminum nitride ceramics are very close to those of silicon wafers, and they have high thermal conductivity. Therefore, substrates made of aluminum nitride are widely used in the electronics industry.
AlN Density
AlN is a covalent bond compound, atomic crystal, diamond-like nitride, hexagonal system, wurtzite crystal structure, non-toxic, white or grey white,The chemical composition is AI 65.81%, N 34.19%, theoretical density 3.26g/cm3.
Why Use Aluminum Nitride Ceramics?
- High thermal conductivity (>170W/m.K), close to BeO and SiC, more than 5 times that of Al2O3;
- The thermal expansion coefficient (4.5 *10-6℃) matches that of Si (3.5-4 *10-6℃) and GaAs (6 *10-6℃);
- Good electrical properties (dielectric constant, dielectric loss, bulk resistivity, dielectric strength);
- Good mechanical properties, higher bending strength than Al2O3 and BeO ceramics, sintering under normal pressure;
- Good light transmission characteristics;
- Non-toxic
Aluminum Nitride Properties
Casting
The tape casting method is a very important ceramic substrate molding process. The AlN powder and the composite binder (composed of dispersant, solvent, binder and plasticizer) are evenly mixed to obtain AlN cast slurry. After degassing and other processes, the slurry is poured into the hopper and passed through the scraper. After opening, a thin layer with uniform thickness and smooth surface attached to the smooth belt is formed, and then dried to prepare a green body with good toughness; after debinding and sintering, an AlN substrate material is obtained. This process is mostly used to make aluminum nitride ceramic plates or substrates.
Dry Pressing
Dry pressing is a process of adding AlN powder pretreated by surfactant modification to a metal mold, and slowly applying pressure to make it a compact green body molding process. The essence is to rely on external pressure and the interaction between AlN powder particles to keep the green body in a certain shape and high density. It is conducive to ceramic sintering, can reduce the sintering temperature, and increase the density of ceramics.
Through the injection molding process, the problem of high hardness, brittleness, and difficult processing of aluminum nitride ceramics is effectively solved, and the precision manufacturing of a variety of micro and complex shapes and high thermal conductivity aluminum nitride products has been successfully realized, especially for small sizes and complex shapes. Aluminum ceramic parts realize high-efficiency production, save raw materials and machining costs, and improve production efficiency.
Injection Molding High Thermal Conductivity Aluminum Nitride Ceramics (IMHTCAN) is based on the injection molding aluminum nitride ceramic process using high-purity, higher-quality aluminum nitride powder.
Mechanical Properties
Properties | Unit | AN |
IMAN |
IMHTCAN |
---|---|---|---|---|
Colour | —— | Grey | Grey | Grey |
Density | g/cm^3 | 3.3 | 3.3 | 3.3 |
Hardness | GPa | 11 | 11 | 11 |
Compressive Strength | MPa | 2100 | 2100 | 2100 |
Flexural Strength | MPa | 450 | 410 | 300 |
Fracture Toughness | MPam1/2 | 3.5 | 2.6 | 2.4 |
Modulus of Elasticity | GPa | 310 | 310 | 310 |
Poissons Ratio | —— | 0.25 | 0.25 | 0.25 |
Thermal Properties
Properties | Unit | AN |
IMAN |
IMHTCAN |
---|---|---|---|---|
Maximum Use Temperature | ℃(No load) | 1350 | 1350 | 1350 |
Thermal Conductivity @ 25°C | W/(mK) | >170 | >170 | >200 |
Thermal Expansion at 40–400°C | 1 x 10-6/°C | 4.5 | 4.6 | 4.9 |
Specific Heat | J/(kgK) | 720 | 720 | 720 |
Thermal Shock Resistance | ℃(Put in water) | 350 | 350 | 350 |
Electrical Properties
Properties | Unit | AN |
IMAN |
IMHTCAN |
---|---|---|---|---|
Dielectric Constant | 1MHz | 8.8 | 8.5 | 8.5 |
Dielectric Strength | ac-kV/mm | >15 | >15 | >15 |
Volume Resistivity @ 25°C | Ωcm | >1014 | >1014 | >1013 |
*The values are typical material properties and may vary according to products configuration and manufacturing process. For more details, Please feel free to contact us.
*Aluminum nitride is easy to be oxidized on the surface, which forms a layer of alumina.This helps to protect the material, but it affects the thermal conductivity (alumina is about 30 W/mK).In an oxidative atmosphere, this occurs at about 700℃.In an inert atmosphere, the layer protects AlN at temperatures as high as about 1350℃.When the temperature is higher than this, bulk oxidation occurs.
What Can AlN Ceramics Be Used For?
- Heat sinks & heat spreaders;
- Electrical insulators;
- Silicon wafer handling and processing;
- Substrates & insulators for microelectronic devices;
- Substrates for electronic packages;
- Chip carriers for sensors and detectors;
- Laser heat management components;
- Molten metal fixtures;
- Packages for microwave devices;
View Aluminum Nitride Substrates & Washer
The common structures of aln ceramic products include AlN substrates, AlN ceramic washers, sheets, etc.
Machining Aluminum Nitride Ceramics
China Ceramics Parts is an expert in machining aluminum nitride ceramics. Since 2013, we have participated and provided more than 3000 kinds of precision ceramic products to hundreds of companies.
We can provide you with technical ceramic processing, ceramic materials, ceramic casting, ceramic metal encapsulation and surface metallization services. We are committed to providing products and services that meet or exceed our customers’ quality requirements.
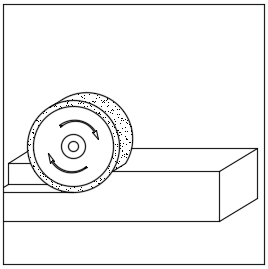
Machining
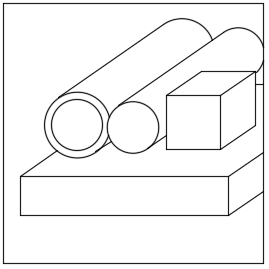
Materials
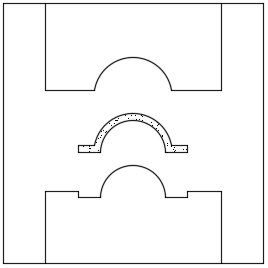
Mould
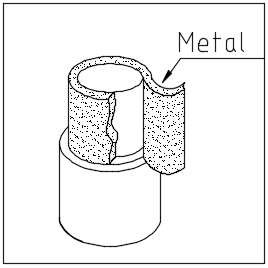
Metallization
Aluminum Nitride Ceramic Manufacturer
China Ceramics Parts is a professional AlN ceramic manufacturer that can meet your technical ceramic needs. We are always happy to use our many years of technical ceramics experience to advise on materials, designs and applications. If you would like to purchase AlN sheet, sheet, washer, bar or custom machined parts, please contact us and each of our experts will be happy to assist you.
Aluminum nitride ceramics have been used in many fields due to their high thermal conductivity, high insulation strength, low dielectric constant and dielectric loss, and excellent resistance to plasma erosion. For example, they are used for chip heat dissipation and support. Ceramic substrates, aluminum nitride ceramic trays used in semiconductor equipment, aluminum nitride etching shields, aluminum nitride evaporation boats for OLEDs, etc. Plastics and resins usually have low thermal conductivity (<0.3W/mk). By adding aluminum nitride powder to plastics or resins, thermally conductive potting compounds and thermal pads with high thermal conductivity (>10W/mk) can be obtained. Used in the packaging field of electronic components.
High thermal conductivity, low expansion coefficient, high strength, high temperature resistance, chemical corrosion resistance, high resistivity, low dielectric loss, is an ideal large-scale integrated circuit heat dissipation substrate and packaging material.
Aluminum nitride ceramics will chemically react with inorganic acids, strong alkalis, water and other liquids and slowly dissolve, so it cannot be directly immersed in such materials. But aluminum nitride can resist most molten salts, including chloride and cryolite.