Advanced Ceramic Forming
At China Ceramics Parts, we utilize a variety of advanced ceramic forming capabilities to create cost-effective advanced ceramic products for our customers. We will negotiate with customers based on factors such as product raw materials, size and precision, and order quantity to determine the best solution that meets customer needs.
Advanced Ceramic Forming Methods
Advanced ceramic forming methods can be divided into dry forming and wet forming. Dry forming includes dry pressing, isostatic pressing, ultra-high pressure forming, powder electromagnetic forming, etc. Wet forming can be roughly divided into two categories: plastic forming and colloidal casting. Plastic molding refers to a molding method in which plastic materials are pressed into rigid molds, including extrusion molding, injection molding, etc.
Our services include: dry pressing, hot pressing, cold isostatic pressing, extrusion, injection moulding (CIM), etc.
Ceramic Injection Molding Process
The first step is to mix the ceramic powder with the polymer binder to form the raw material. After the raw material is plasticized, it is injected into the cavity under high pressure. After injection molding, the product is in the green stage and we may process it as needed. The next step is to remove the adhesive by heat or chemical means in a furnace. The final step is sintering, where the product is made.
Advanced Ceramic Injection Molding(CIM)
Ceramic injection molding (CIM) has advantages for mass production of ceramic products with high dimensional accuracy and complex shapes. It has been widely used in aviation, automobile, machinery, energy, optical communication, life medicine and other fields.It has significant advantages over traditional molding methods:
- Cost-effective technology;
- Suitable for high volume production runs;
- Achieving very high size requirements (≤1% size);
- Reduce manufacturing costs.
At present, the materials suitable for ceramic injection molding are: alumina, zirconia, silicon nitride, aluminum nitride, etc.
Advanced Ceramic Injection Molding Examples
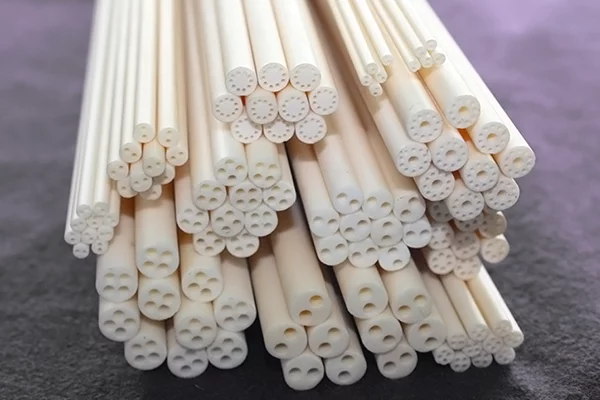
Ceramic Extrusion Die Forming
China Ceramics Parts offers ceramic tubes or rods made from extrusion dies, and can be customized to size and complex shapes according to customer needs. Typically, such products are composed of alumina ceramics or mullite for functions such as high temperature protection or electrical insulation.This process is widely used in the preparation of ceramic furnace tubes, electromagnetic insulators, catalyst carriers, heat exchange tubes, honeycomb ceramic carriers for exhaust filtration, and the like.
Ceramic Extrusion Die Forming Examples
Ceramic Hot Die Casting
Ceramic hot die casting can form complex-shaped ceramic products, with high dimensional accuracy and almost no subsequent processing, so it is the main process for making special-shaped ceramic products. In addition, the production cost is relatively low because the production equipment is inexpensive, easy to operate, and high in production efficiency.
However, due to the low molding pressure of ceramic hot die casting, it is easy to lead to low product density, high porosity, and many internal defects. This process is not suitable for the preparation of large-scale ceramic products.
Ceramic Hot Die Casting Examples
Ceramic Isostatic Pressing
The so-called isostatic pressing generally refers to cold isostatic pressing (CIP), which is a method of obtaining ceramic products by using the incompressibility of the liquid medium to uniformly transmit pressure and pressurizing from all directions. . According to the different molding process, it can be divided into two forms: wet bag type and dry bag type.
Advantages of ceramic isostatic pressing:
- The pressure is transmitted from all directions, the density distribution of the green compact is uniform, and the green compact strength is high;
- The green body has high density, less uniform defects, and the firing shrinkage is lower than the general dry pressing;
- It can press parts with concave, slender and other complex shapes;
- Small friction loss and low molding pressure;
- The mold cost is low.
Application of ceramic isostatic pressing:
- Preparation of high-performance alumina ceramic raw materials, such as ceramic tubes, ceramic rods, ceramic plates, etc.;
- Preparation of high-performance alumina ceramic parts blanks of various shapes;
- Alumina ceramic vacuum switch arc interrupter “tube shell” series products, alumina and zirconia ceramic plungers, and large-size zirconia ceramic cylinder liners for oil drilling, etc.
Ceramic Dry Pressing
Dry pressing, also known as molding, is one of the most commonly used molding methods. Dry press molding is to put the granulated powder with good fluidity and suitable particle gradation into the metal mold cavity, and apply pressure through the indenter. The bulk particles are rearranged and deformed and compacted to form a ceramic green body with certain strength and shape.
Advantages of ceramic dry pressing:
- The process is simple, the operation is convenient, the cycle is short, the efficiency is high, and it is easy to implement automatic production;
- The green body has high density, accurate size, small shrinkage, high mechanical strength and good electrical properties.
Application of ceramic dry pressing:
It is especially suitable for the preparation of various ceramic products with small cross-sectional thickness, such as ceramic sealing rings, ceramic valve cores for valves, ceramic linings, ceramic linings, etc.
Advanced Ceramic Molding Manufacturer
China Ceramics Parts is an expert in the production of advanced ceramics. Since 2013, we have participated in and provided more than 3,000 precision ceramic products to hundreds of companies.
We can provide you with ceramic machining, ceramic materials, ceramic casting, ceramic metal packaging and surface metallization services. We are committed to providing products and services that meet or exceed customer quality requirements.